Pistol Machining Project Plans
The following is a post by my friend Jason, who is not a regular contributor, but has posted in the past on our 3D magazine printing project. I thought this would be an interesting addition, and a demonstration of how technology is making gun control a virtual impossibility. Below is his post.-SebastianI’ve been meaning to try this for a while now (using the AR-15 lower receiver solid model from ), but I wanted to do it using all open source software, and was having trouble finding something that could generate tool paths from the AR-15 model. PyCAM seemed to be the best bet, but whenever I tried it on very complex model it would very quickly use up all the memory (8GB of ram plus 8GB of swap) and bring the computer to a screeching halt.I recently had a project at work where I needed to make a much simpler part, and not wanting to go back to using BobCAD under Windows, I gave HeeksCAD and PyCAM a try. It worked out pretty well, and in the process I discovered and fixed a memory leak in PyCAMPyCAM is still horribly inefficient in its memory usage, but with the memory leak fixed and a new computer with 16GB of ram I was finally able to generate decent toolpaths for the AR-15 lower.The equipment/software:.
A small Taig desktop CNC mill. EMC2 for controlling the mill. HeeksCAD for model manipulation. PyCAM for toolpath generation.So now I’m all set to give this a try, but I can’t find the block of aluminum I had intended to use. Ads by media player removal. But I did have a block of Delrin left over from an earlier project, and Delrin should be strong enough to handle a.22 cal upper.
So I’m trying to make a delrin lower first for use with a.22 cal upper, and if that works I’ll order some aluminum and make another lower for use with a.223 upper.Note that I’m not an expert in material properties (nor a machinist) so don’t take the above statements to mean that its safe to fire an AR-15 made of Delrin. Do at your own risk.The original block of Delrin.After a first pass rough cut with a 0.25″ diameter end mill.After a second pass using a 0.125″ end mill and a much smaller grid size.After a finishing pass with a 0.125″ ball nose mill.Now things are going to get a little complicated. I’m going to have to make some sort of jig to hold the part in place while I machine the other side. I would NOT, repeat NOT shout any thing out of a firearm made from Delrin. But I would use Delrin as a quick proof of concept and parts fitting if you are going to make a real firearm at some point. Its is a lot cheaper then quality Alu, or Steel, and should be able to machine it a lot quicker(say 2 or 3x tool movement(not RPM) speed).
Machining Projects Blueprints
And i am all for testing out tool pathing and what not on cheap stuff before running a good block of quality metal. And it would make a perfect platform for testing jig setup and what not.:P.
CHEN MAGWELL GEN2 INSTALLATIONThe Gen2 is machined as one piece, integral with the Mainspring Housing. The entire bottom of the full size pistol frame is shortened by.300”, by machining, to accommodate the magwell. No length or width is added to the pistol. Concealability, portability, and the overall handling of the pistol is not compromised.
If you can conceal a standard 1911, you will be able to conceal a Chen Magwell’ed 1911 with the exact same ease. The Chen Magwell Gen2 is attached to the pistol frame via the Mainspring Housing Pin, which is relocated from its original position.The Chen Magwell Gen2 adds two Side Impact Reinforcement Tabs, which snugly engage against the sides of the pistol frame, and provide a tremendous amount of lateral support to the magwell so it will not twist from any side impact.The Chen Magwell Gen2 allows for the removal of stuck magazine by providing access to the toe of the magazine so that the magazine can be forcefully extracted in the event it becomes stuck in the pistol.
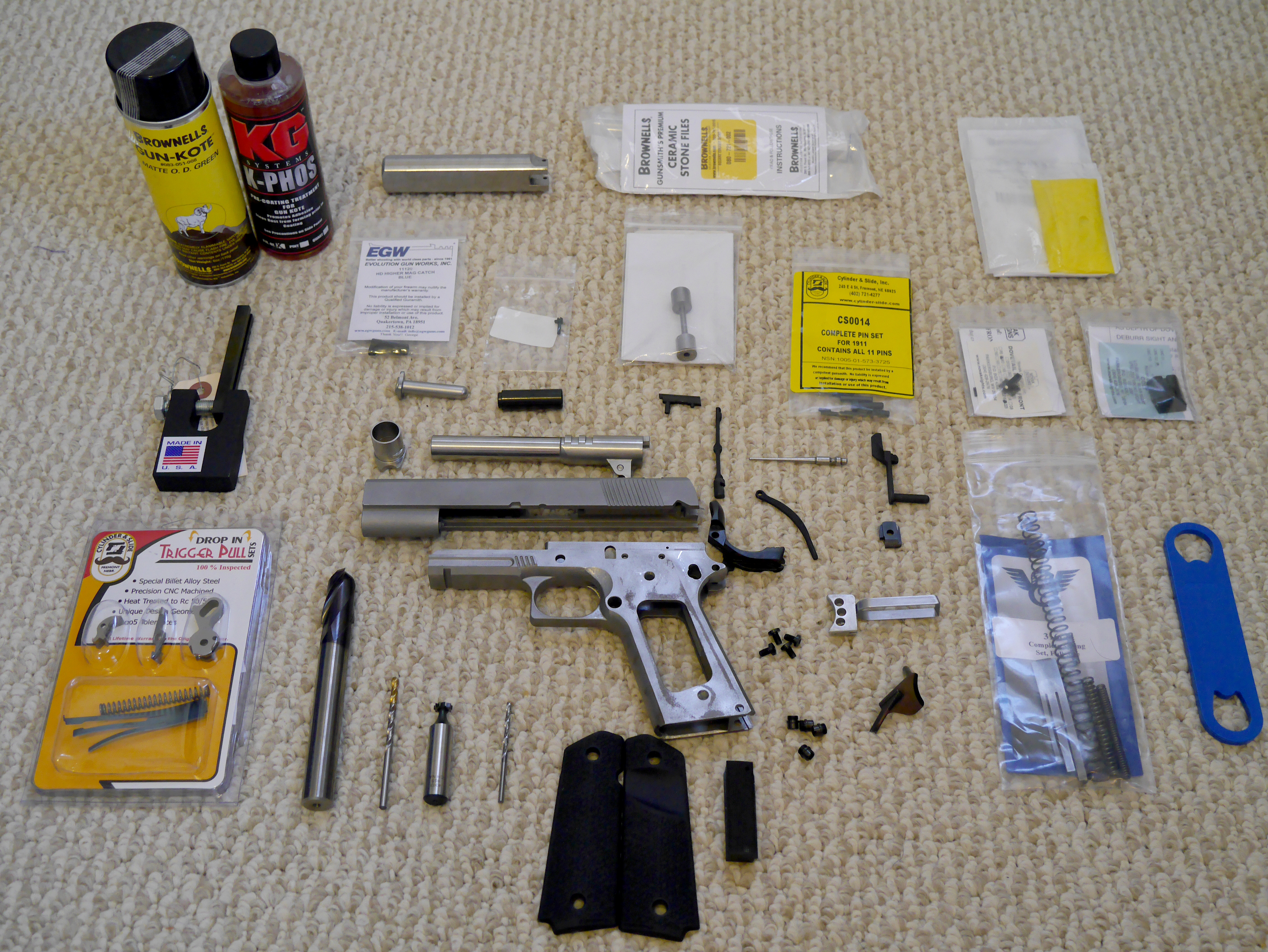
This is made possible by 1.) front magwell geometry which has been considerably reduced compared to traditional weld-on magwells and 2.) a pronounced access notch has been machined in front.The Chen Magwell Gen2 delivers speed and consistency while reloading under stress. Using sophisticated CAD design and CAM driven machining, the magwell opening is opened up as wide as possible without adding bulk. The entry angle is optimized for the smoothest reloads possible. The Chen Magwell Gen2 is custom installed, contoured, blended, and dehorned. A generous roundbutt is machined and hand sculpted into the part itself, enhancing shooting and carry comfort. The proprietary Chen BevelBlock™ is a block of extra material in a key location at the rear of the magwell, which allows a seamless, gap-free blend with the pistol.Our custom installation includes a dramatic, custom blend of the magwell into the pistol frame itself.
This makes the transition from magwell to pistol even more effortless in function and more seamless in appearance. The blend goes as far up into the pistol as possible, assuring the most efficient entry angle.The installation is completed with custom fitting of double diamond G10 grips which are made for us by our friends at VZ Grips.
Please note if you wish to change grips in the future, VZ Grips will soon supply the 'Chen Magwell Cut' as an option. They will come shortened for the magwell, with relief cuts for the Side Impact Reinforcement Tabs, and just a little extra material for final fitting.The Chen Magwell Gen2 Installation service does NOT include our ProTrac™ checkering treatment. If you desire ProTrac™ checkering as well, please see the Gen2 and ProTrac™ Package below.Pistols must be stainless steel or carbon steel.

Pistol Machining Project Plans Template
Currently we are not accepting aluminum alloy frames. Nickel plated firearms must have the nickel finish stripped/removed prior to machining. Bobtailed frames are not suitable.The following brands are suitable for our machining services: Colt, Springfield, Dan Wesson, Kimber, Wilson, Nighthawk, Ruger, Remington, JEM, and Caspian, with full length grip frames (i.e.
Government or Commander/Champion sized). If your frame is not on this list, please drop me an email. The Chen Maxbevel™ treatment transforms the bottom of your pistol into an ergonomic, elegant masterpiece of effectiveness. The Chen Maxbevel™ treatment gives the largest available magwell bevel without an add on part.The Chen Maxbevel™ is seamlessly cut into the mainspring housing as far to the rear as possible for reliably fast reloads.

This is done using our unique, proprietary Chen Mainspring Housing. The Chen MSH allows for this seamless cut to be performed without the unsightly gap which is common to other attempts at enlarging the bevel to the rear with a standard mainspring housing. Beyond just enlarging the opening, the entire area is hand blended and dehorned into an ergonomic, flowing unit. The front of the mag well is cut and shaped to eliminate the sharp corners on stock pistols, which can cut the shooter during fast reloads.RoundButt As part of the Maxbevel™ treartment, your pistol will receive our 'RoundButt' treatment, which provides a significant increase in comfort while both shooting the pistol, and carrying it concealed. To accomplish this, the back heel of the pistol, to include the frame and mainspring housing, is generously blended and radiused into an integrated, comfortable contour.
Combined with our ProTrac™ and HighCut, the Roundbutt is part of what makes the pistol feel as though it 'melts' comfortably in your hand. This combination is available as part of the Chen Maxbevel™ and ProTrac™ Package, see below.
The chen magwell gen2 and protrac packageThe Chen Magwell Gen2 and ProTrac package includes the following:Installation and custom blend of the Chen Magwell Gen2 (Magwell included)ProTrac™ checkering of the frontstrapHigh Cut frontstrapProTrac™ checkering of the Chen Magwell Gen2 mainspring housingPistols must be stainless steel or carbon steel and in stock, unmodified condition. Currently we are not accepting aluminum alloy frames. Nickel plated firearms must have the nickel finish stripped/removed prior to machining.Of course, the frontstrap must be smooth and not have any checkering or other frontstrap treatment already cut.
Bobtailed frames are not suitable.The following brands are suitable for our machining services: Colt, Springfield, Dan Wesson, Kimber, Wilson, Nighthawk, Ruger, Remington, JEM, and Caspian, with full length grip frames (i.e. Government or Commander/Champion sized). If your frame is not on this list, please drop me an email. Pistols must be stainless steel or carbon steel.
Currently we are not accepting aluminum alloy frames. Nickel plated firearms must have the nickel finish stripped/removed prior to machining. Bobtailed frames are not suitable.The following brands are suitablefor our machining services: Colt, Springfield, Dan Wesson, Kimber, Wilson, Nighthawk, Ruger, Remington, JEM, and Caspian, with full length grip frames (i.e. Government or Commander/Champion sized). If your frame is not on this list, please drop me an email.
Refinishing OptionsStainless steel pistols- satin matte finish over entire pistolStainless steel pistols- satin matte finish lower end onlyStainless steel pistols- satin matte finish slide onlyCarbon steel pistols- satin matte blue finish over entire pistolCarbon steel pistols- satin matte blue finish lower end onlyCarbon steel pistols- satin matte blue finish slide only.Note that certain models of 1911s which appear to be black (most notably Kimber) are actually a mixture of stainless steel and carbon steel parts. As such, these pistols cannot be blued. An alternate coating such as Cerakote should be applied.Note that certain models of stainless steel 1911s (such as Ruger), have black parts such as slides stops, thumb safeties, and grip safeties. These black parts will NOT be included in the satin matte stainless finishing. They will remain as they came to us.